Critical Process Dual-Walled Vessels: Your Comprehensive Guide
Roben, Mfg, Inc. is a leading manufacturer of critical process dual-walled vessels, specializing in the design, fabrication, and supply of high-quality vessels that meet the most stringent safety and process requirements. With our expertise and state-of-the-art manufacturing facilities, we deliver reliable and efficient dual-walled vessel solutions for critical processes across various industries.
Contact Us
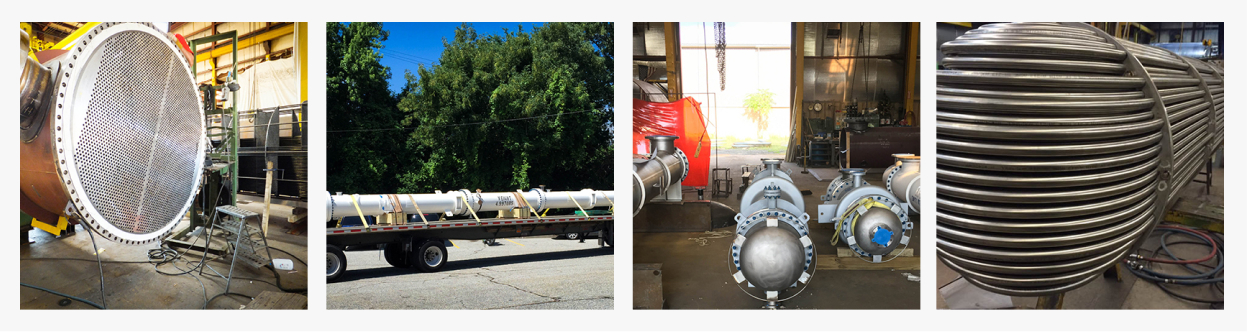
What is a Critical Process Dual-Walled Vessel? A critical process dual-walled vessel is a container designed with two separate walls or shells, providing an extra layer of containment and often allowing for temperature control or added safety measures. These vessels are crucial for processes where contamination prevention, precise temperature control, or additional safety barriers are essential.
Why Choose Critical Process Dual-Walled Vessels? Critical process dual-walled vessels are essential for various reasons
- Enhanced Safety: They provide an additional layer of containment, crucial for hazardous materials.
- Temperature Control: The space between walls can be used for heating or cooling, ensuring precise process temperatures.
- Contamination Prevention: Dual walls reduce the risk of external contamination or product leakage.
- Process Integrity: They ensure stable conditions for sensitive processes or reactions.
- Regulatory Compliance: They often meet stringent regulatory requirements for critical processes.
Critical Process Dual-Walled Vessel Specifications and Characteristics: At Roben, Mfg, Inc., we offer a range of critical process dual-walled vessel options to suit your specific needs. Our vessels are designed to provide maximum process control and safety, including
- Customizable Inner and Outer Wall Materials
- Precise Temperature Control Capabilities
- Advanced Leak Detection Systems
- High-Integrity Sealing and Welding
- Customizable Jacket Designs (full or partial)
- Integration with Process Control Systems
Our critical process dual-walled vessels are available in different configurations, including
- Vertical Dual-Walled Tanks
- Horizontal Dual-Walled Tanks
- Spherical Dual-Walled Vessels
- Dual-Walled Reactors
- Dual-Walled Storage Tanks
- Dual-Walled Transport Vessels
We also offer various enhancements and accessories to meet your specific requirements, such as
- Advanced Agitation Systems
- Specialized Nozzle Configurations
- CIP/SIP Systems for Sanitary Applications
- High-Performance Insulation
- Customized Instrumentation and Controls
- Specialized Surface Finishes
Critical Process Dual-Walled Vessel Types: Roben, Mfg, Inc. manufactures a comprehensive range of critical process dual-walled vessel types, including
- Pharmaceutical-Grade Reactors
- Bioprocessing Fermenters
- Chemical Synthesis Reactors
- Cryogenic Storage Tanks
- High-Purity Material Storage Vessels
- Sterile Processing Tanks
- Temperature-Sensitive Material Transport Vessels
Materials: We work with a range of specialized materials to fabricate critical process dual-walled vessels that meet your specific requirements. Our materials include
- High-Grade Stainless Steels (e.g., 316L, 904L)
- Hastelloy and Other Nickel Alloys
- Titanium and Titanium Alloys
- Glass-Lined Steel
- Special Polymer Linings
- Zirconium for Highly Corrosive Applications
Certifications and Standards: Our critical process dual-walled vessels are designed and manufactured in accordance with the most stringent industry standards and certifications, including
- ASME Boiler and Pressure Vessel Code
- FDA cGMP Guidelines
- EU GMP Standards
- ISO 9001 Quality Management System
- PED (Pressure Equipment Directive) for European Compliance
- ATEX Directive for Explosive Atmospheres (where applicable)
We utilize advanced 3D modeling and finite element analysis (FEA) software to ensure optimal design and performance of our dual-walled vessels.
Industries Served: Our critical process dual-walled vessels serve a range of industries that require precise process control and high levels of containment, including
- Pharmaceutical Manufacturing
- Biotechnology
- Fine Chemical Production
- Food and Beverage Processing
- Semiconductor Manufacturing
- Aerospace
- Nuclear Industry
- Specialty Materials Production
Applications: Our critical process dual-walled vessels are suitable for various applications, including
- Sterile Pharmaceutical Production
- Bioreactor Systems for Cell Culture
- High-Purity Chemical Synthesis
- Cryogenic Material Storage
- Temperature-Sensitive Material Processing
- Clean Room Manufacturing Processes
- Hazardous Material Containment
- Ultra-Pure Water Storage
- Specialty Gas Handling
- Aseptic Food Processing
- Active Pharmaceutical Ingredient (API) Manufacturing
- Nuclear Waste Containment
- Semiconductor Wet Processing
- High-Value Material Transport
- Catalyst Production and Storage
- Highly Exothermic or Endothermic Reactions
Frequently Asked Questions (FAQs)
1. What are the primary advantages of dual-walled vessels over single-walled vessels?
Dual-walled vessels offer enhanced safety through secondary containment, better temperature control capabilities, and reduced risk of contamination or leakage.
2. How is temperature control managed in dual-walled vessels?
Temperature control is typically achieved by circulating heating or cooling fluids through the space between the inner and outer walls, allowing for precise temperature regulation.
3. What types of processes are best suited for dual-walled vessels?
Dual-walled vessels are ideal for processes requiring precise temperature control, high purity, sterile conditions, or handling of hazardous materials.
4. How is the integrity of the dual-wall system monitored?
Integrity is often monitored through leak detection systems in the interstitial space, pressure monitoring, and regular inspections. Some systems may include continuous monitoring capabilities.
5. Can dual-walled vessels be used for both high-pressure and low-pressure applications?
Yes, dual-walled vessels can be designed for a range of pressures, from vacuum to high pressure, depending on the specific application requirements.
6. What materials are commonly used for the inner and outer walls?
Common materials include stainless steel, specialized alloys like Hastelloy, glass-lined steel, and in some cases, the inner wall may have a special polymer lining for corrosion resistance or purity.
7. How do cleaning and sterilization processes work for dual-walled vessels in sanitary applications?
Many dual-walled vessels designed for sanitary applications include Clean-in-Place (CIP) and Steam-in-Place (SIP) systems, allowing for thorough cleaning and sterilization without disassembly.
8. What are the maintenance requirements for critical process dual-walled vessels?
Maintenance typically includes regular inspections of both walls, integrity checks of the interstitial space, maintenance of temperature control systems, and calibration of monitoring instruments.
9. How do dual-walled vessels contribute to energy efficiency in processing?
The double-wall design often provides better insulation, reducing heat loss or gain and thus improving energy efficiency in temperature-controlled processes.
10. Can existing single-walled vessels be converted to dual-walled vessels?
While possible in some cases, converting a single-walled vessel to a dual-walled design is often complex and may not be practical or cost-effective. It’s usually better to design a dual-walled vessel from the ground up.
For more information about our critical process dual-walled vessel solutions or to request a quote, please contact Roben, Mfg, Inc. today. Our experienced team is ready to assist you in selecting the right critical process dual-walled vessel for your specific application.