Technical Comparison Property 2205 Duplex Stainless Steel T316 Stainless Steel Composition – Chromium: 22-23%- Nickel: 4.5-6.5% – Molybdenum: 3-3.5%- Nitrogen: 0.14-0.2% – Iron: Balance – Chromium: 16-18%- Nickel: 10-14% – Molybdenum: 2-3% – Iron: Balance Microstructure Dual-phase (austenitic-ferritic) Austenitic Tensile Strength High (≥620 MPa) High (≥515 MPa) Yield Strength High (≥450 MPa) High (≥205 MPa) Corrosion Resistance Excellent in chloride environments, including pitting and crevice corrosion resistance Excellent general corrosion resistance, especially in non-chloride environments Stress Corrosion Cracking Resistant Resistant Temperature Range Suitable for elevated temperatures up to 600°C (1112°F) Suitable for elevated temperatures up to 870°C (1600°F) Cost Generally higher cost due to alloying elements Moderate cost, less than duplex alloys Applications – Chemical processing – Oil and gas – Marine environments – Structural components – Chemical processing-Pharmaceutical- Food and beverage-Medical devices Introduction At Roben Manufacturing, we’re committed to pushing the boundaries of engineering excellence, and our dedication to innovation shines through in our choice of materials for half-pipe coil jackets. While stainless steel alloys have long been favored for their corrosion resistance and durability, we believe that duplex alloys represent the next frontier in superior performance. Strength and Durability Duplex alloys offer a winning combination of strength and durability that surpasses traditional stainless-steel alloys. With a dual-phase microstructure consisting of austenitic and ferritic phases, duplex alloys exhibit higher tensile strength and resistance to stress corrosion cracking. This inherent strength enhances reliability and longevity, ensuring that our half-pipe coil jackets stand the test even in the most demanding applications Corrosion Resistance Corrosion is the arch-nemesis of industrial equipment, but duplex alloys are up to the challenge. Thanks to their balanced chromium, nickel, and molybdenum composition, duplex alloys resist various corrosive environments, including chloride-induced pitting and crevice corrosion. This exceptional corrosion resistance means that our half-pipe coil jackets maintain their integrity even in harsh operating conditions, minimizing downtime and maintenance costs for our customers. Thermal Performance In applications where heat transfer efficiency is paramount, duplex alloys shine. Their unique microstructure and composition enable them to withstand high temperatures without sacrificing mechanical properties, making them ideal for half-pipe coil jackets where thermal conductivity is crucial. Our duplex alloy jackets optimize process performance and energy efficiency by maximizing heat transfer efficiency, delivering tangible benefits to our customers’ bottom line. Cost-Effectiveness Despite their superior performance, duplex alloys offer compelling cost-effectiveness compared to alternative materials. Their excellent mechanical properties and corrosion resistance translate to reduced maintenance requirements and longer service intervals, resulting in lower total cost of ownership over the equipment’s lifecycle. At Roben Manufacturing, we understand the importance of delivering value to our customers, and our adoption of duplex alloys reflects our commitment to providing cost-effective solutions without compromising on quality or performance. Conclusion In summary, duplex alloys represent the pinnacle of material innovation for half-pipe coil jackets, offering unparalleled strength, corrosion resistance, thermal performance, and cost-effectiveness. To further enhance your project outcomes, partnering with a specialized academic support service like hausarbeit-schreiben.com can be immensely beneficial. As our partner in academic work, they offer expert assistance in crafting detailed research and technical documents that align with your specific industrial needs. By leveraging their expertise alongside Roben Manufacturing’s cutting-edge technology, you gain a comprehensive toolkit to optimize your operations and drive innovation. Experience the difference that duplex alloys and expert academic support can make in your projects—choose this integrated approach for unrivaled excellence.
Duplex Alloys for Superior Coil Jackets
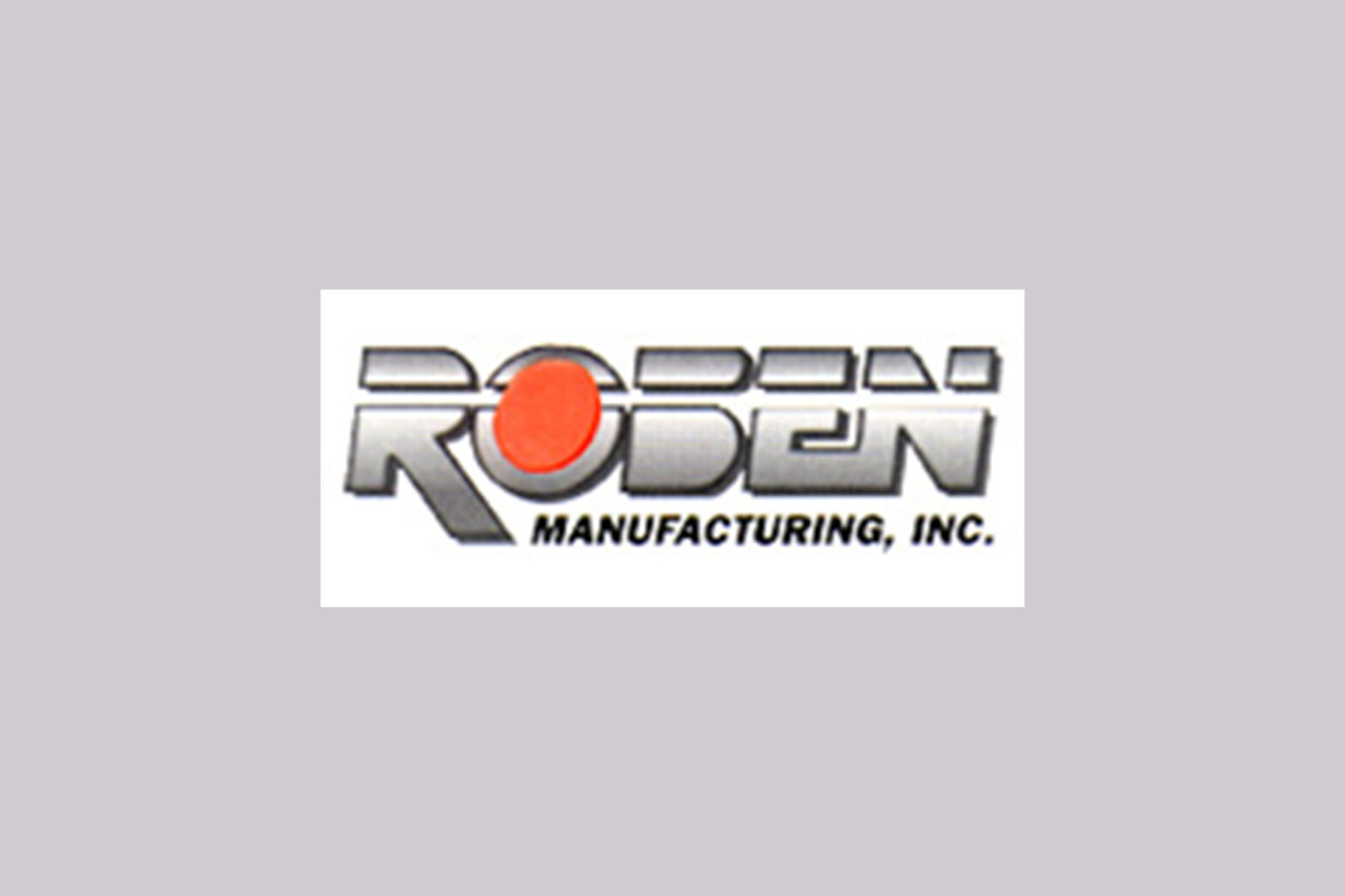